The operations teams at our D.C. and Northern Virginia warehouses are the backbone of our work, ensuring that more than 60 million meals reach neighbors across the DMV each year. Every day, they orchestrate a well-choreographed dance of logistics, moving food in and out of warehouses to meet the region’s needs.
That choreography hits a crescendo in the months from October to December: our operations team is tasked with moving a far greater volume of food during the holiday season, when so many of our gatherings happen around food.
Take a look at how the different roles within our operations team come together each morning to keep food moving in and out the door. But first, here are a few key pieces of warehouse lingo:
- Order: A request placed by a partner or site specifying the quantity and type of food they need.
- Pallet: A group of food items stacked on a wooden platform, making it easier to store and handle with equipment like forklifts.
- Loading Dock: The designated area where trucks are loaded and unloaded at the warehouse.
- Receiver: A warehouse team member responsible for managing incoming food shipments.
- Puller: A warehouse team member who collects and organizes food items to fulfill orders for the next day’s deliveries.
5 a.m.: Hitting the Ground Running
Before the sun rises, our warehouse is already alive with action. Forklifts zip around and the operations team greets the day with a mix of focus and camaraderie.
Our team of drivers arrives at 5 a.m., to receive their assignments and start loading their trucks. With lists in hand, they move between the dry storage racks, cooler, and freezer, gathering the items needed to fulfill that day’s orders. Packing the trucks is like playing Tetris: the drivers must carefully arrange pallets to maximize space and ensure safe transport.
Dushane Clark, a driver who has been with the food bank for nearly 13 years, explains that while the usual schedule runs from 5 a.m. to 2 p.m., during the busy season, it can stretch to 5 p.m. “One stop could mean unloading 20 to 30 pallets of food,” he says. Last month alone, the food bank’s drivers completed 929 deliveries, exceeding the 700 to 800 deliveries typical of average months.
As the trucks are loaded, they start pulling out of the warehouse by 7 a.m., each one bound for partner sites and direct distribution locations across the region.
Managing the Influx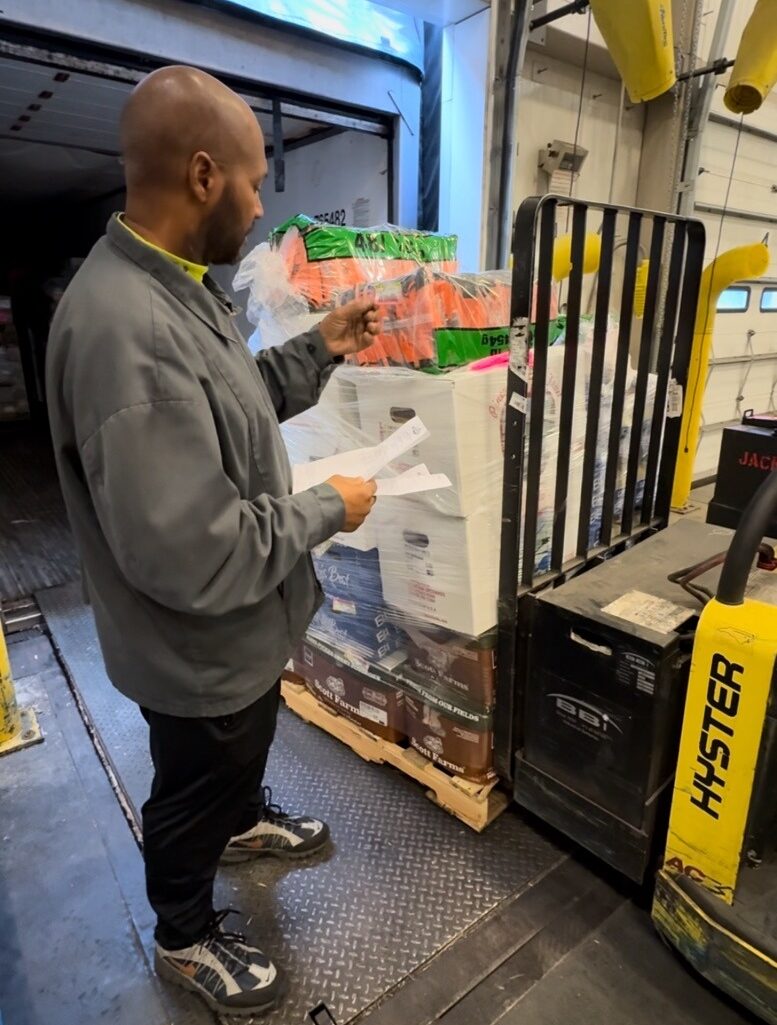
As delivery trucks head out, the receiving team gets ready for the day’s incoming shipments. During an average month, the warehouse receives about five truckloads of food daily. In the busy season, that number can double, with over 4 million pounds of food arriving in a single month.
The receivers start by reviewing the day’s schedule and coordinating dock assignments for incoming trucks. When a truck arrives, they perform a quality check, ensuring the food was handled safely.
After inspection, the team unloads the truck and counts and dates every single pallet before passing it along to the warehouse associates for storage in the freezer, cooler and racks for dry goods.
Keeping Inventory in Check
Once the food is unloaded, the warehouse and inventory associates step in. Their job is to scan each item into the system and distribute it to its proper location. This process ensures accurate inventory counts and smooth order fulfillment later.
With a growing focus on stocking culturally familiar foods like masa flour and a commitment to sourcing from local farmers, the inventory team is also handling a wider variety of options than ever before. Carl Robinson, a warehouse associate with 12 years of experience, shares that he’s seen a significant expansion in the variety of foods we offer, particularly fresh produce.
9 a.m.: Prepping Tomorrow’s Orders
The pulling team arrives by 9 a.m. to pack orders for the following day. Looking at their assigned orders, they gather everything needed. Sometimes this consists of entire pallets, and other times it could be individual boxes.
For pullers like Carlton Colding, who has been with the team for over a decade, the work is labor-intensive but rewarding.
“People are surprised I enjoy it, but I like knowing my job helps get food to people in need.”
—Carlton Colding, Warehouse Associate
In an average month, the team fulfills 30 to 40 orders daily, but during the busy season, that number can climb up to 60. They stay until every order is complete, because without their work, the next day’s deliveries won’t happen.
The Bigger Picture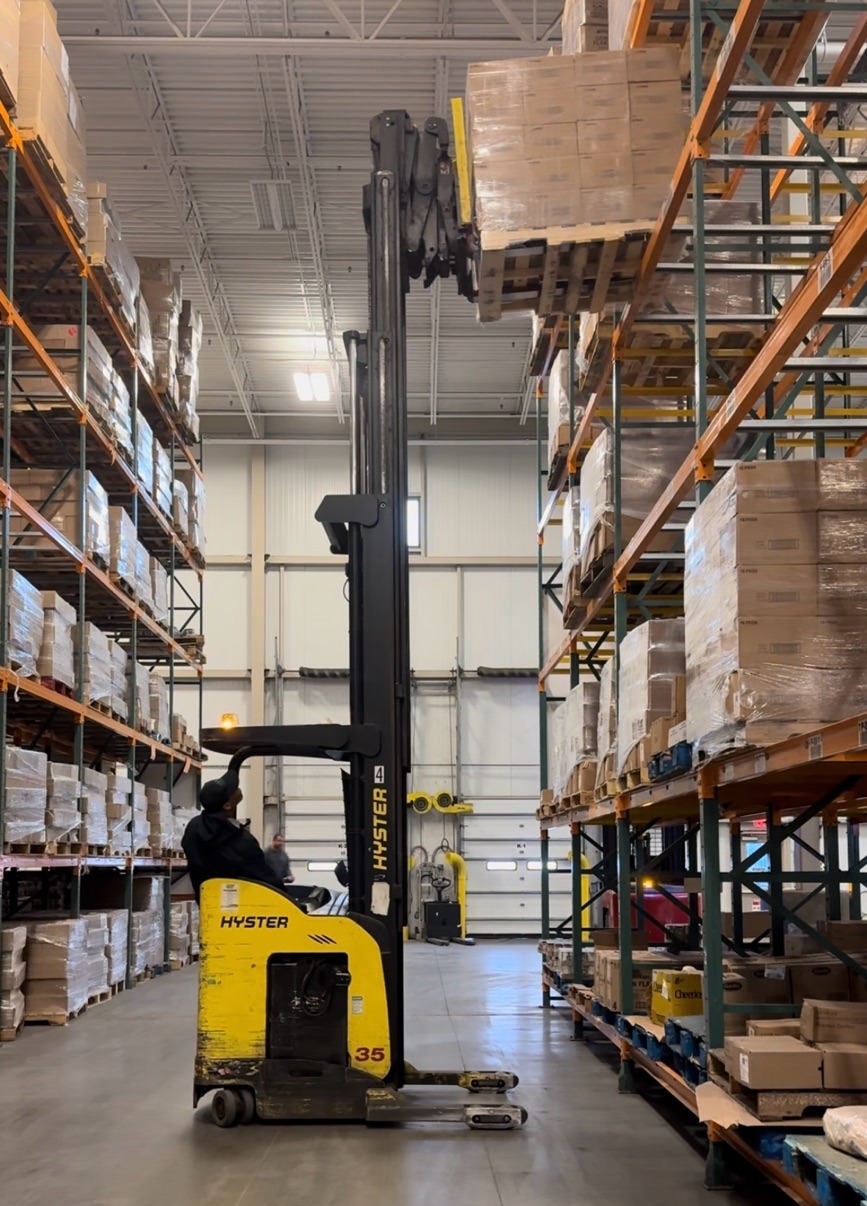
Throughout the warehouse, every team member has a critical role to play.
The opening of the expanded Northern Virginia facility in Lorton has also been a game-changer this season. Before that larger facility reopened, most food deliveries came to our DC headquarters, with food for Virginia-based distributions then delivered separately to our NOVA warehouse. With orders for the Northern Virginia region now fulfilled directly from Lorton, the DC team has fewer orders to handle, lightening their load during the busiest month.
Hunger exists year-round, and our operations team remains at the center of our mission to make sure families across the region have the nutritious food they need.